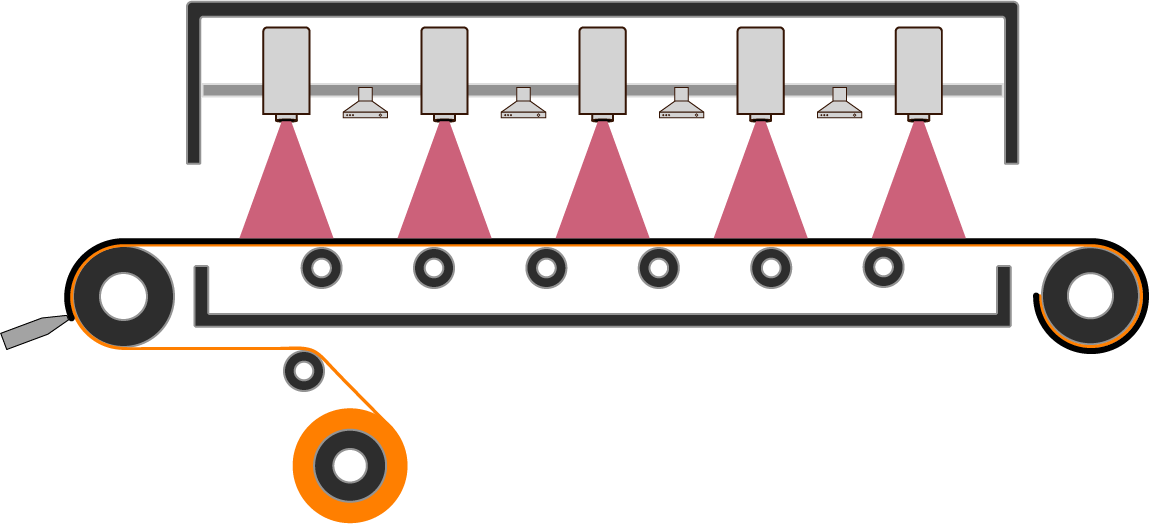
Battery drying consumes a lot of energy. It is estimated that a Lithium-ion battery manufacturing site needs 50-65 kWh of electricity per kWh of battery capacity.This drives up manufacturing costs. The drying process uses up 26% of the total energy consumption and 21% of the total capital and operational expenditure.Lithium-ion battery manufacturing commonly use convection oven drying in addition to other methods such as infrared (IR) drying and vacuum drying. For this reason it is a top priority to find more energy efficient methods to dry the slurry.
Compared with traditional convection reflow ovens our lasers offer several advantages:
- Precisely controlled heating to target specific areas it heats sensitive components without affecting adjacent materials.
- Rapid drying by delivering high-intensity energy achieve faster drying times.
- Energy efficient by only heating areas that need to be heated, minimizing waste.
- Customized drying profiles for different battery designs, materials and optimization.
It is expected that by replacing convection ovens with lasers we can save large amounts of energy and manufacturing costs.
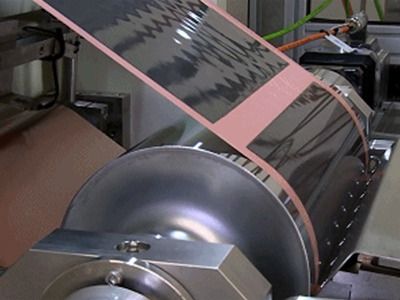
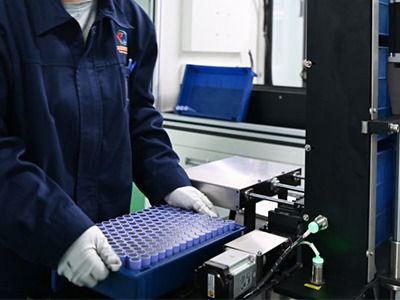
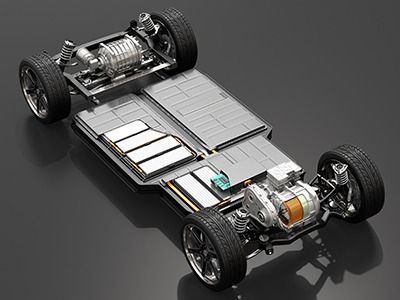
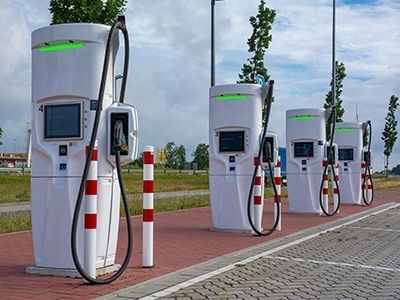
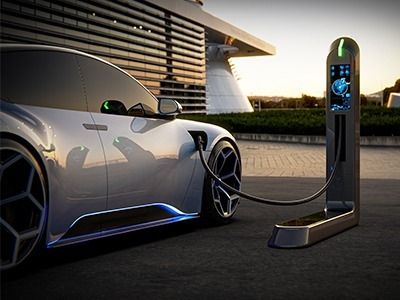
With the development of new energy vehicles, the battery market is also growing rapidly.