1.Can achieve both welding and preheating simultaneously
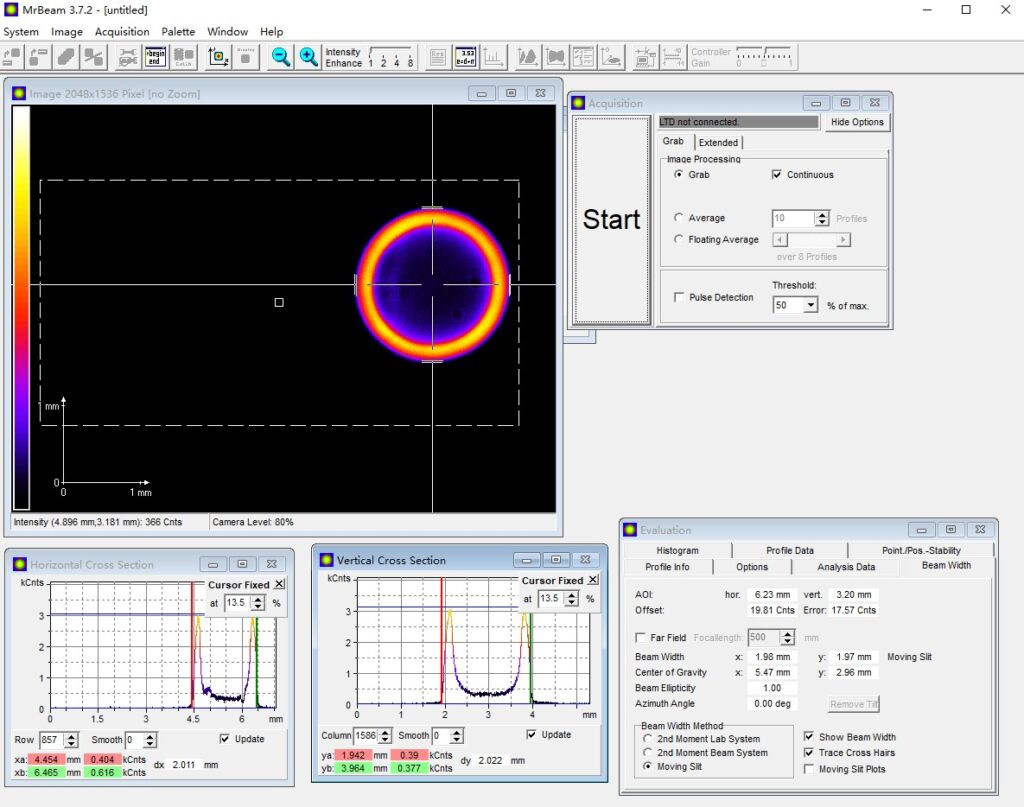
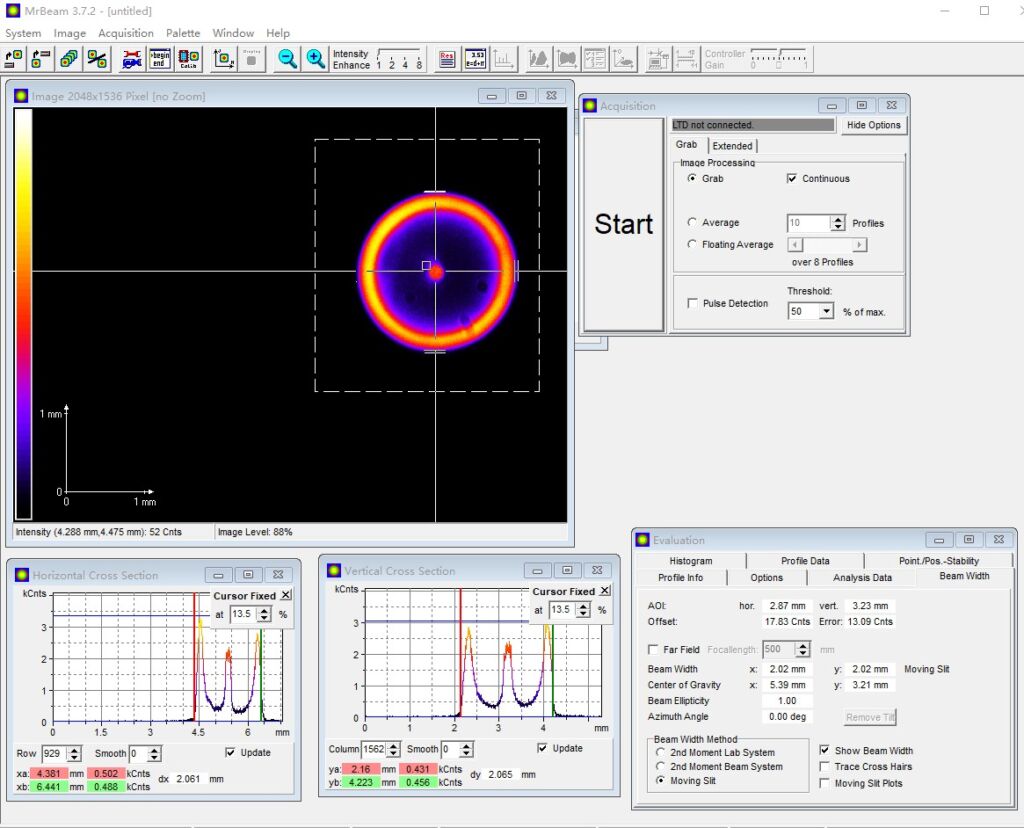
2.Adaptive Spot
3.Temperature control
Lascon® controller is connected to the laser. It allows for fast, precise,and accurate material surface temperature control.
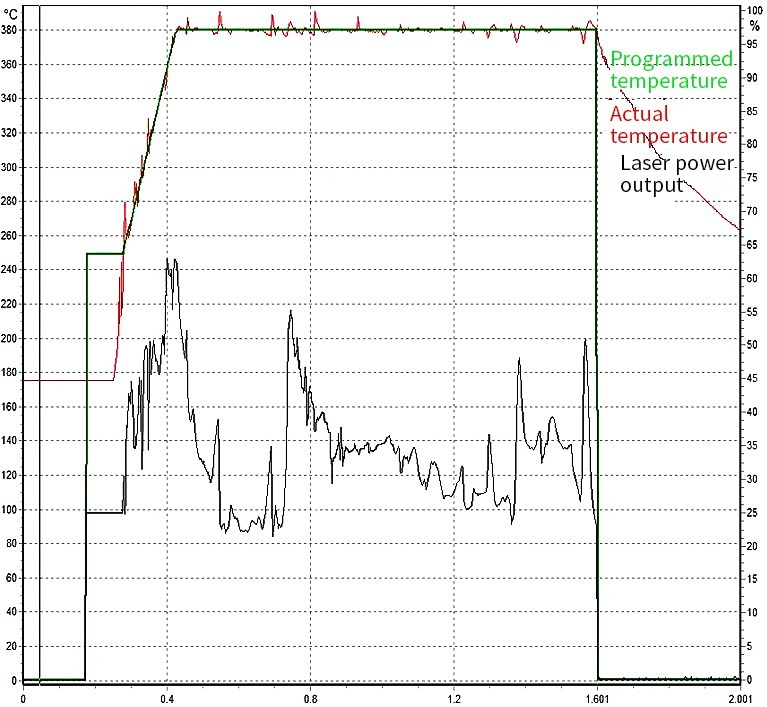
Lascon® controller is connected to the laser. It allows for fast, precise,and accurate material surface temperature control.
Laser system specifications | |||
Serial Number | Parameter | Unit | Details |
1 | Laser power | W | 30, 60, 100 |
2 | Wavelength | nm | 975 |
3 | Power adjustment range | % | 0~100 |
4 | Pilot light | – | Yes |
5 | Fiber core diameter | µm | 200 or customized |
6 | Numerical aperture | – | 0.22 |
7 | Fiber length | m | 3, 5 or customized |
8 | Connector | – | SMA905 or D80 |
9 | Input voltage | V | 200~240(50-60Hz) |
10 | Operating mode | – | Continous wave (CW) |
11 | Maximum modulation frequency | Hz | 20000 |
12 | Control mode | – | External control touch screen, RS232 serial port, analog AD |
13 | Dimensions (L×W×H) | mm | 354 * 133 * 298 |
14 | Weight | Kg | 10.5 |
15 | Cooling method | – | air cooling |
16 | Working temperature | ℃ | 15-30 |
17 | Storage temperature | ℃ | 5-50 |
18 | Cooling requirement | – | 10 cm open space around it |
19 | Laser safety class | – | DIN EN 60825-1, class 4 |
Laser head specifications | |||||
Serial Number | Parameter | Unit | Special laser head | ||
1 | Power limit | W | up to 200 | ||
2 | Spectral range | nm | 975nm (peripheral)+915nm (central) | ||
3 | Optics | – | 1″, AR coated, focal length on request | ||
4 | Fibre connector | – | FSMA905, D80, LLK-A (connection of various fibre laser collimators available) | ||
5 | Fibre diameter | µm | 100 – 600 | ||
6 | Numerical aperture | – | 0.22 | ||
7 | Pilot laser | – | Class 2. Wavelength 650nm +/- 10nm, via fibre coupled pyrometer | ||
8 | Ambient temperature | ℃ | 5-55 for operation, no condensation | ||
9 | Dimensions | mm | 164.5 * 73 * 323.2 | ||
10 | Weight | kg | 4.2464 | ||
11 | Protection | – | IP50 | ||
12 | CE label | – | According to EU directives for electromagnetic immunity | ||
13 | Conformity | – | The RoHS Directive 2011/65/EU of 2011-06-08 with supplement from 2015-03-31 is fulfilled |
Controller specifications
|
|||
Serial Number
|
Parameter
|
Unit
|
Details
|
1
|
Temperature range
|
℃
|
100 – 2200
|
2
|
Spectral range
|
µm
|
1.65 – 2 / 1.65 – 2.5
|
3
|
Accuracy (e=1, t90=1s, T=25℃)
|
–
|
< 1500℃ 0.3% +/- 2K
|
4
|
Repeatability
|
–
|
0.1% +/- 1K
|
5
|
Resolution
|
℃
|
0.1
|
6
|
Response time
|
ms
|
0.1
|
7
|
Emissivity
|
–
|
0.01 – 1
|
8
|
Analog output
|
V
|
0-10 (16Bit configurable using software)
|
9
|
Power supply
|
–
|
24V DC, max. 2A
|
10
|
Data storage
|
–
|
internal, 500.000 processes, 255 process control scripts
|
11
|
Optical fibre length
|
m
|
3, 5 or customized
|
12
|
Ambient temperature
|
℃
|
max 40
|
13
|
CE label
|
–
|
According to EU directives for electromagnetic immunity
|
14
|
Conformity
|
–
|
The RoHS Directive 2011/65/EU of 2011-06-08 with supplement from 2015-03-31 is fulfilled
|
15
|
Software
|
–
|
LASCON® software
|
16
|
Position
|
–
|
Coaxial
|
LASCON® is the process monitoring system with probably the largest distribution in the laser industry. More than 1500 users worldwide in industry and research monitor and regulate their laser processes with LASCON®.
The LASCON Process Manager uses the infrared or 2 color pyrometers to measure the temperature on the workpiece 10,000 times per second and compares the measured temperature with a specified setpoint temperature. From the difference, the systems calculated the rated power for the laser system. This laser system is controlled by an analogue signal so that any laser system can be used with analog voltage power input. But it can also control inductors and other heat sources. The processes are monitored, stored and visualized. The process data of each process can additionally be exported automatically to an external server. Easily programmable scripts can be used to set monitors around setpoint temperatures to create an error signal if the measured temperature is not within the temperature monitor. Especially for laser soldering, the solder wire feeder can also be parameterized and started by software from the script.