LASCON® is the process monitoring system with probably the largest distribution in the laser industry. More than 1500 users worldwide in industry and research monitor and regulate their laser processes with LASCON®.
The LASCON Process Manager uses the infrared or 2 color pyrometers to measure the temperature on the workpiece 10,000 times per second and compares the measured temperature with a specified setpoint temperature. From the difference, the systems calculated the rated power for the laser system. This laser system is controlled by an analogue signal so that any laser system can be used with analog voltage power input. But it can also control inductors and other heat sources. The processes are monitored, stored and visualized. The process data of each process can additionally be exported automatically to an external server. Easily programmable scripts can be used to set monitors around setpoint temperatures to create an error signal if the measured temperature is not within the temperature monitor. Especially for laser soldering, the solder wire feeder can also be parameterized and started by software from the script.
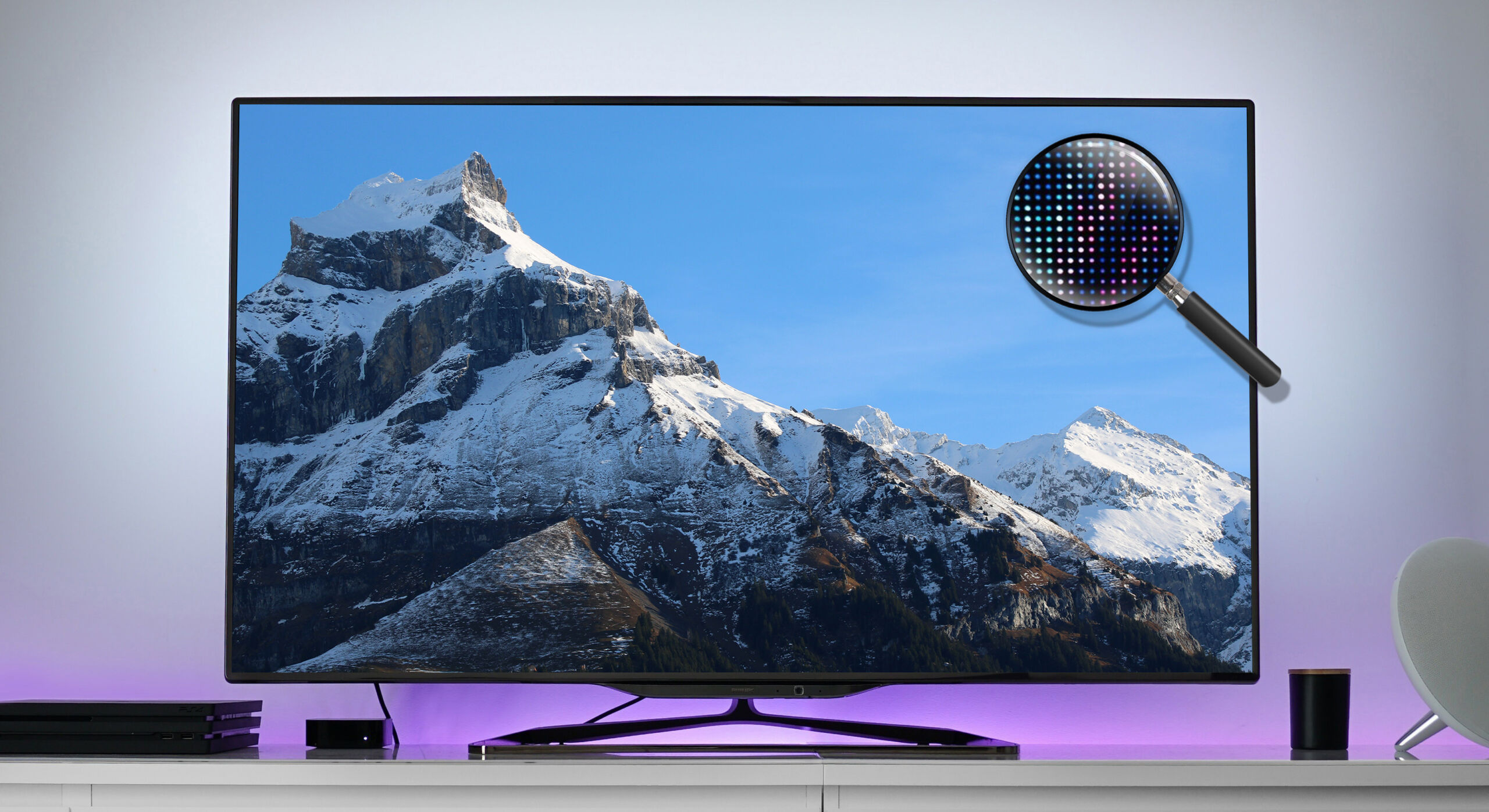
MiniLED repair
MiniLED repair is a necessary step in the product manufacturing process, which mainly involves repairing MiniLED components that are damaged during the reflow process due to solder defects, misalignment, burning, and other reasons. There are two heating processes during the MiniLED repair process: first, the faulty component must be removed from the PCB through heating. Secondly, clean the solder pads to ensure correct formation of solder joints, and then place the new miniLED in the desired position and solder it onto the PCB. In order to meet the needs of the MiniLED repair process in the appeal, we provide a standard tool – LBS mini laser system.