Laser soldering is an advanced welding technology that uses laser as a heat source. After precise optical processing, it quickly heats low melting point solder (such as tin wire or solder paste) to melt and fill the small gaps between the components to be welded, forming a solid solder joint. Thermostatic soldering can be combined with sensors to measure the temperature of the soldering point at high speed while soldering. At the same time, compared with the target temperature curve, after algorithm processing, feedback control is used to output laser energy, thereby achieving the set temperature curve and achieving the best soldering effect.
Laser soldering has more advantages than soldering iron soldering:
- Remote welding, non-contact, no load on the substrate
- Accurate positioning, adaptable to complex surfaces, without interference
- High laser efficiency, fast tin melting, full solder joints, and minimal thermal impact on the surrounding area of the solder joints
- The light spot can reach the micrometer level and is suitable for needle tip solder joints
- Almost no maintenance required
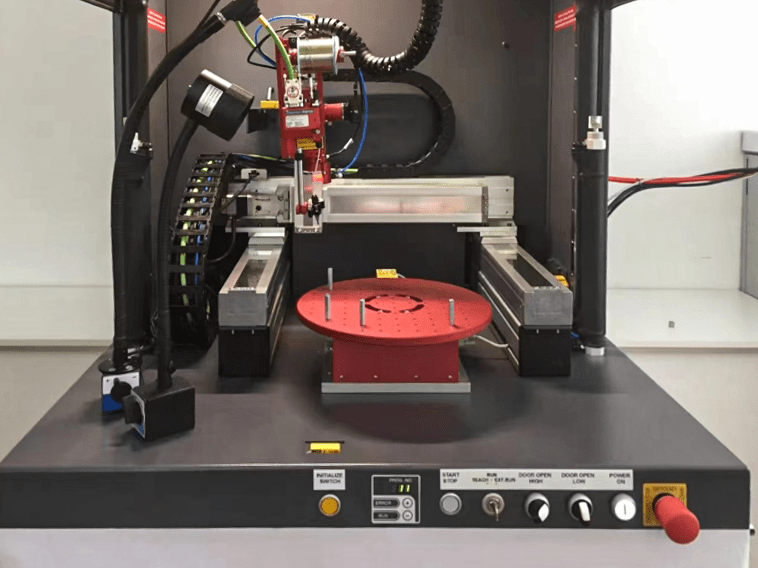
Our laser welding system
Our company focuses on the research and innovation of laser welding technology. Compared with most laser soldering equipment on the market, our laser soldering system has the following advantages:
- High speed closed-loop temperature control can achieve fast and accurate surface temperature control of materials
- Equipped with a wire feeder, it can achieve precise wire feeding
- Customized solution – Each laser soldering system can be optimized according to customer needs for application optimization
- Dual spot technology allows laser systems to have two adjustable spot sizes, spacing, and energy ratios
- Blue light laser
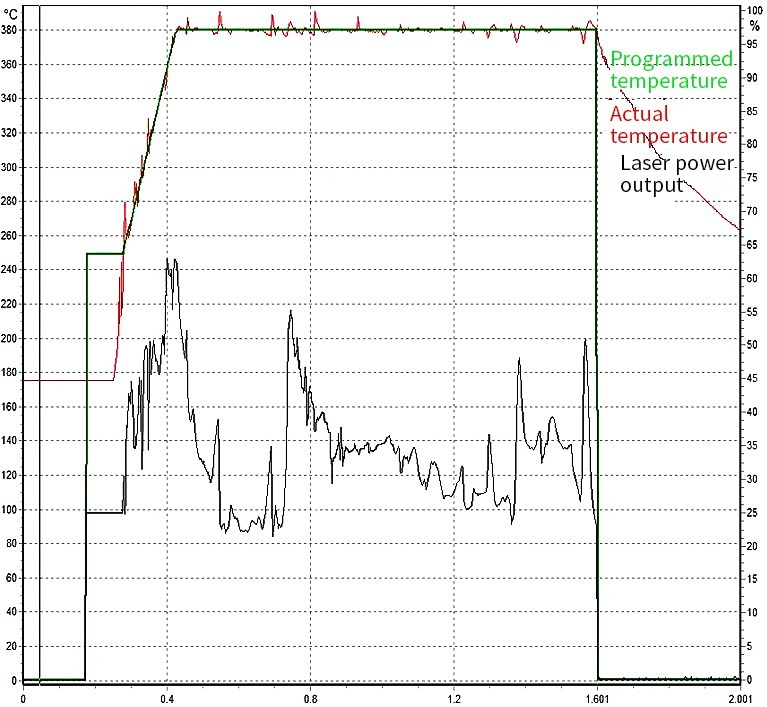
The figure shows that the laser system changes the laser temperature through high-speed closed-loop control of the pyrometer feedback, achieving the predetermined temperature curve.